Trends related to the energy transition are shifting global demand for refined products and affecting feedstock slates, forcing petroleum refiners to embrace adaptation and flexibility
Demand for fossil fuels has remained strong in the years after the COVID-19 pandemic, but the pressure for lowering greenhouse-gas (GHG) emissions also remains high. The momentum for an energy transition to low-carbon fuels and renewable energy is now sufficient enough that it will have a growing impact on demand for refined products into the future. Combined with other factors, such as geopolitical conflicts, natural disasters and government environmental policies, the push toward lowering CO2 emissions requires petroleum refiners to build flexibility into their operations to adapt to changing demand profiles for products, and changing feedstock slates (Figure 1).
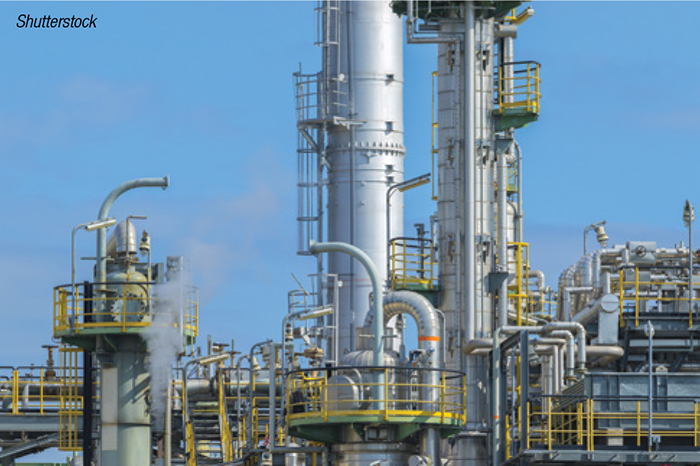
FIGURE 1. Decarbonization goals and the need to adjust to changing product demand is prompting refiners to build flexibility into their operations
Significant opportunities exist for refiners to offset medium- and long-term declines in demand for traditional transportation fuels by changing their product portfolios to include more lower-carbon fuel alternatives, such as biofuels and hydrogen, and more chemical precursors. Between the rising demand for low-carbon fuels and the slowing, but still positive, demand for traditional fuels, petroleum refiners currently have a window of opportunity to position themselves for the future without disruption of financial stability.
“The most competitive refiners typically have at least one of the following advantages: cheap crude, captive product market, high complexity and conversion unit capacity, integration with petrochemicals, or strong logistics,” explains Austin Lin, a principal analyst at Wood Mackenzie (Edinburgh, U.K.; www.woodmackenzie.com), so it is along these themes that refinery investment will likely occur. “Modernization and equipment upgrades [will be] targeted toward improving jet [fuel] and diesel yields (via a hydrocracker) given the higher margins and expectations of longer-lasting demand,” Lin suggests.
“The industry has demonstrated a willingness to invest in new technologies and projects to decarbonize, but the economic incentive remains a key part of that transition,” Lin says.
Comments from Shell Catalysts and Technologies (SC&T; Houston; www.shell.com) align with the idea of building flexibility and conversion capacity into refineries. “Flexibility will be key as refiners process a wider variety of feed sources and convert those to a more diverse product range,” the company says, adding that refineries could see a move toward more specific molecule targets, rather than distillation ranges for fuels. “Building flexibility and efficiency around conversion assets will be critical to adapt to changing landscapes,” Shell C&T says. This includes future work with non-conventional feeds, such as pyrolysis oils and recycled plastics.
“Petrochemical integration also remains a key trend, with many newer facilities and expansions in the Middle East and Asia aiming to maximize flexibility across the value chain,” Wood Mackenzie’s Lin says.
Refined products demand shift
Recent industry analyses have looked at the forecasted demand for transportation fuels in different regions. For example, a trend report from Deloitte Consulting (London, U.K.; www.deloitte.com) [1] projects global oil demand will slow down in the long term, rising annually by only 0.4 million bbl/d until 2027. Meanwhile, the report says global biofuels demand is projected to rise by 44% between 2022 and 2027, as it increasingly substitutes for petroleum-based products. In addition, the share of electric vehicles in global car sales is expected to range between 62% and 86% by 2030, according to research by RMI (Basalt, Colo.; www.rmi.org) [2]. Rising sales will be led by Northern Europe and China, and will be driven by policy, RMI says.
Wood Mackenzie’s Lin says, “In the medium- to long-term view, European and North American markets are expected to see peak oil demand in the next few years, as vehicle electrification and policy changes outweigh normal growth. Meanwhile, the Asian market is expected to continue growing, with new refining capacity continuing to come online in the region.”
“This shift will place rationalization pressure on Western refiners as they look to increasingly compete in export markets, making the business case for reinvestment challenging for many facilities,” Lin remarks.
Chris Jablonski, vice president of downstream technology at Chevron Corp. (San Ramon, Calif.; www.chevron.com) points out the unevenness of the demand changes. He says while Chevron sees oil and gas continuing to play a critical role in meeting global transportation demand for the foreseeable future, there are headwinds for gasoline, including electrification of the vehicle fleet. Thus far, however, the trends in electrification have generally met the company’s expectations. “There will be certain times when [electrification] accelerates and other times when it slows down,” Jablonski says, and “there are [geographic] areas where electrification will be widespread, and others where it will not.”
Crude petroleum availability is also impacting refinery operations. “Crude slates remain a concern, particularly in Europe and Asia, where the combination of Russian sanctions and OPEC+ production cuts have reduced the availability of medium and heavy barrels in the market,” Wood Mackenzie’s Lin says. “The shift to lighter crude diets has challenged refiners from a yields perspective, which has been a contributing factor to high refined product crack spreads.”
Renewable fuels
Growing demand for fuel products sourced from materials other than conventional crude petroleum is prompting refiners to increase production of renewable diesel and sustainable aviation fuel (SAF), but difficulties remain. “Renewable fuels are a hot topic in the industry right now, with significant capacity coming online in both North America and Europe in recent years,” Lin says, “However, economics and feedstock availability remain a challenge for continued growth — currently, renewable fuels are not profitable to produce without significant policy support, with the feedstocks themselves being more expensive in many instances than the conventional fuels they are replacing.”
Based on current differences among the regions in regulatory environment and stated carbon-emissions-reduction goals, Europe is expected to be a global hub for SAF, while the U.S. is expected to lead in renewable diesel, Lin says.
Looking ahead, he explains, “While current policies remain supportive for existing capacity, additional incentives may be needed to spur further investment, as producers are forced to consider lower-margin feedstocks due to availability issues. As a result, there is an expected ceiling for the renewable-fuels market, where additional capacity is uneconomic or politically challenged (for example, because of agricultural feedstock competition against food supply concerns).”
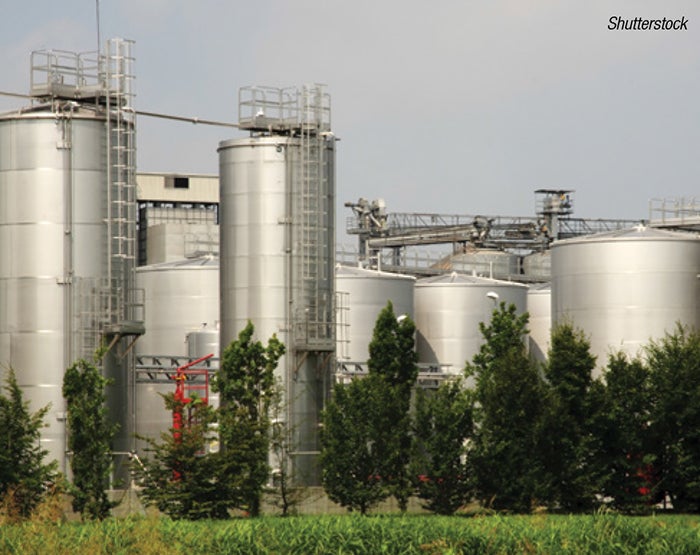
FIGURE 2. Demand for renewable diesel and sustainable aviation fuel (SAF) is growing, but there are concerns over feedstock availability
The Deloitte report says, “Refiners may grapple with the task of effectively leveraging subsidies and grants for strengthening the biofuel supply chain. Therefore, considering strategic steps, such as securing a consistent feedstock supply, handling grade fluctuations, and optimizing transportation expenses and emissions, can facilitate the efficient expansion of biofuels and set refiner performance apart.”
As an example, the report cites the joint venture between Marathon Petroleum Corp. (Findlay, Ohio; www.marathonpetroleum.com) and ADM (Chicago, Ill.; www.adm.com) for establishing a specialized soybean-processing facility to generate refined vegetable-oil feedstock for renewable-diesel production. The facility (Green Bison Soy Processing), opened in late 2023 in North Dakota.
For its part, Chevron is also developing capacity for producing renewable diesel and SAF using the hydrotreated esters and fatty acids (HEFA) route. The company is putting a lot of effort into developing new catalysts to improve the HEFA process and increase its efficiency, Chevron’s Jablonski says. “We are also repurposing existing equipment for making renewable fuels, while also preserving the swing-back capability to go back to making conventional fuels, if customer demand warrants it,” he says.
Simultaneously, Chevron is also working to develop feedstocks for renewable fuels that lower carbon intensity and help improve scalability, Jablonski notes, in addition to studying how to obtain fuels from new oil-yielding crops, lignocellulosic biomass and algae. “We’re trying to align that work with catalyst and process development, so the activities complement each other,” he says.
In one example, Jablonski points to a 2023 project on low-carbon-intensity gasoline, in which Chevron partnered with automaker Toyota to make gasoline that Chevron says is comparable to battery-powered cars on a lifecycle basis, with respect to carbon intensity. Chevron’s renewable gasoline blend, made from both biomass and conventional components, contains more than half renewable materials, the company says, claiming it can reduce lifecycle CO2 emissions by more than 40% compared to traditional gasoline. Last year, the drop-in fuel replacement was used in a demonstration project involving three Toyota vehicles driving from Mississippi to Texas (Figure 3).
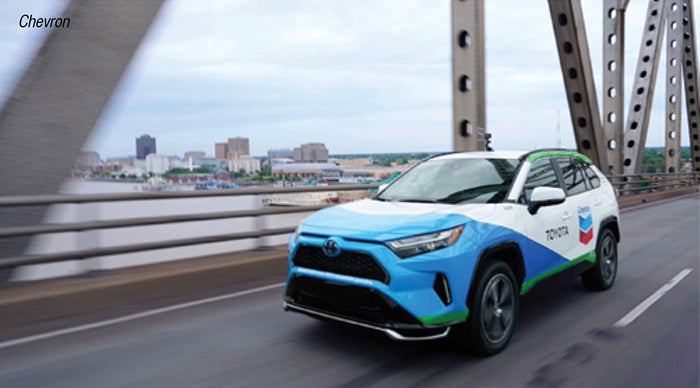
FIGURE 3. Last year, a demonstration project involving Chevron and Toyota used a blend of renewable and conventional gasoline to power a roadtrip across southern U.S. states
In other recent renewable-fuel developments, the Italian energy company Eni SpA (Rome; www.eni.com) in January 2024 confirmed that it will move ahead with plans to convert its facility in Livorno into a biorefinery. And in April of this year, Phillips 66 (Houston, Texas; www.phillips66.com) announced progress in converting its San Francisco refinery into the Rodeo Renewable Energy Complex. The facility now processes only renewable feedstocks, producing approximately 30,000 bbl/d of renewable diesel. Repsol S.A. (Madrid, Spain; www.repsol.com) announced in April the start of large-scale production of renewable fuels at its industrial complex in Cartagena (Spain).
Turning to SAF, TotalEnergies SE (Paris; www.totalenergies.com) and China Petroleum and Chemical Corp. (Sinopec; Beijing; www.sinopec.com) signed a preliminary agreement in March 2024 to jointly develop a SAF production unit at a Sinopec refinery in China. The planned unit will have the capacity to produce 230,000 tons of SAF per year, and will process local waste cooking oils and animal fats.
Decisions and digitalization
For refinery leaders, the pace of change for decision making has accelerated greatly in the last decade and the evolution of technology has also accelerated. “The frequency and pace at which you have to make decisions is much faster now than at any time in the past,” Chevron’s Jablonski says, “so we need to accelerate decision-making, but we also need to maintain flexibility to be able to meet long-term investment challenges and maintain viability in the long term.”
Making investment decisions that strike a balance between maintaining the current security of supply and operation with flexibility for the energy transition is among the top three current refinery challenges, agrees SC&T.
To address the challenges, an area of focus has been digitalization tools, such as artificial intelligence/machine learning (AI/ML) and digital twins. Jablonski says, “We’ve seen great potential for AI/ML for predictive maintenance to improve operational availability and streamline turnarounds,” and AI has also been great for materials development R&D for catalysis, he adds. The company has also seen value from developing a digital twin program, Jablonski notes.
Shell C&T says digitalization (of unit monitoring, for example) has led to better and faster access and exchange of data. “We can make data-based decisions and recommendations for optimization much faster and effectively. This improved data exchange has enabled a faster feedback loop for improving catalyst developments and predictive modeling,” the company says.
Further, SC&T says “[AI] and improved computing analytics have improved our ability to monitor, model and develop new technologies for refining. We employ machine learning techniques to accelerate our catalyst development and targeting. We also use advanced computational modeling to better understand the interaction of catalyst active sites with reactant molecules.”
Jade Rodysill, the global and Americas chemicals and advanced materials industry leader at EY (New York, NY; www.ey.com), says $1 billion had been invested in AI technologies by the chemicals industry as of 2022, but by 2032, the total will exceed $17 billion, with at least $1.5 billion aimed specifically at generative AI technology.
“There are a lot of good use cases for AI … but a concern is data — there are plenty of data, but it needs to be contextualized and trusted to be useful in AI applications,” Rodysill says.
Wood Mackenzie’s Lin says “Digital tools are still in their infancy in manufacturing, with many companies working to identify where they can add value. For now, much of the focus has been on reliability, and leveraging technology to better schedule predictive maintenance to avoid downtime.”
And on the process side, “the integration of economic modeling with process-control schemes has been an ongoing journey, as refiners move from base layer to advanced process control,” Lin explains. “The next step as part of a digital journey is to incorporate larger-scale economic models with unit operations, enabling control schemes that span multiple process units and employ more sophisticated economic optimizers,” he says.
Rodysill says AI can already be effective in demand planning and optimizing plant yields more holistically than what was possible in the past. Also, AI has the ability to eliminate human bias in forecasting, he adds.
Chevron’s Jablonski cites the example of real-time optimization (RTO). “In the past, RTO has been done with a systematic, phased plan with steps, but today, we can do it more holistically across the full value chain and more continuously also, from feedstock selection, to process, to the response to pricing and demand changes in the markets.”
The attention on digitalization tools is also prompting the industry to develop employees with the necessary skill set for taking advantage of these technologies. For example, Chevron has been developing digital skills in their engineer cohort through a Digital Scholars Program. To achieve the necessary combination of digital skills, including knowledge of data science, with a basis of domain knowledge in refining and processing, the company has been sending Chevron engineers to get master’s degrees in data science from top universities. “It’s a significant commitment, but it’s worth it,” Jablonski says.
Technology and operations
Shifting feedstocks and product demand also influences refinery technology. Wood Mackenzie’s Austin Lin says “Refining technology is largely in an optimizing phase, with improvements being incremental rather than step changes given the maturity of the industry. The bigger shift is more in the deployment of existing technologies, with newer crude-to-chemicals facilities challenging the historical role of a refinery and instead pushing for [maximum] conversion of heavy material into higher value chemical products.”
“The importance of flexibility for refiners drives the technology innovations,” says SC&T. “We focus on equipment improvements and catalyst advancements that allow for the processing of more complex feed slates with improved yields of desired products.”
For example, the company says refiners now have the ability to process heavy and difficult feeds, such as de-asphalted oils that were previously downgraded. “This is enabled by improvements in reactor internals for efficient flow and filtering, as well as improved catalysts that handle contaminant metals and drive desired reactions,” the company says. It also points to additional technologies that are available to improve the efficiency of hydrogen usage, improved product separation and better heat integration.
Refinery operators are also challenged by escalating operating costs and maximizing asset uptime. Chevron’s Jablonski says, “For complex process facilities, like refining, operational availability is paramount,” and it can manifest in improved turnarounds at a refining site.
Wood Mackenzie’s Austin Lin says “Refiners are in the midst of a very heavy maintenance season globally right now as they try to catch up on years of deferred maintenance due to both COVID related cost cutting and high margins over the last several years.”
Catalysts
Catalysis remains a key area where new product generations continue to unlock new value for refiners by allowing for longer cycle lengths and improved yields, for example.
SC&T says: “We continue to develop catalysts and technologies that enable flexibility of operation. Another aspect of feedstock is that there is more variability in the daily crude diet and less consistency of types/sources of feedstocks. The available feeds tend to be from extremes of heavier/more difficult or lighter/easier without as many middle options — this further emphasizes the need for flexibility of operations.”
In a recent example of a new catalyst offering, Evonik Industries AG (Essen, Germany; www.evonik.com) has launched a catalyst that improves sulfur removal performance for refinery fuel. The technology, known as OctaMax, consists of uniquely selected NiMo (nickel-molybdenum) and CoMo (cobalt-molybdenum) catalysts regenerated and enhanced at optimal conditions for use in cracked gasoline hydrodesulfurization (HDS) units. Evonik says this cost-effective solution maximizes sulfur removal and improves octane-level retention to meet current gasoline pool requirements.
Octamax reduces potential landfill waste by regenerating spent catalysts that can be re-used. This reduces reliance on fresh catalysts, helping to save valuable raw materials – and supporting refineries’ sustainability efforts.
Jignesh Fifadara, Global Director of HPC Catalysts at Evonik Catalysts and responsible for sustainability issues in this field, says: “The worldwide push for lower sulfur content in gasoline is putting refiners under pressure to comply with new limits. They are being challenged to find new ways to optimize performance and profitability, while operating units at higher severity.
“Octamax presents a high-performance and cost-effective solution for Fluid Catalytic Cracking [FCC] gasoline post-treatment units, allowing refiners greater flexibility.”
The product offers equal or better octane selectivity to alternative fresh catalysts and allows refiners to lower sulfur in gasoline without impacting target cycle length.
Octamax can be used by refineries processing FCC Naphtha that are looking to maintain or improve octane levels, while producing ultra-low sulfur gasoline. Its application is also suitable for refineries looking to maximize sulfur credits, by taking advantage of improved catalyst HDS activity.
References
1. Chronis, A., Hardin, K. and Mittal, A., 2024 oil and gas industry outlook, Deloitte Consulting, www2.deloitte.com/us/en/insights/industry/oil-and-gas/oil-and-gas-industry-outlook.html.
2. RMI, EVs to surpass two-thirds of car sales by 2030, press release, Sept. 14, 2023, www.rmi.org.